Machine inspection plays a key— yet often overlooked — role in a complete and effective uptime-focused strategy. In this context, you may ask, “What is machine inspection?”
As a dedicated practice, machine inspection refers to scheduled, purposeful, proactive equipment checks that are carefully designed to identify possible issues and forecast necessary maintenance needs. By gauging machine health at regular intervals, the facility is able to address potential issues more quickly, reduce unplanned maintenance events, and more effectively plan for inventory and MRO needs.
Ignoring the importance of industrial machinery inspections can lead to several negative consequences.
These may include:
- Increased unplanned downtime
- Reduced service life of equipment
- Excessive costs for emergency repairs and parts
- Inefficient and unsafe equipment operation
Machine inspection, explained
Here, we will introduce the tasks that play a part in machinery inspections, the personnel who should perform inspections and recommended intervals for inspection scheduling.
What does machine inspection entail?
Inspections may comprise a range of tasks for equipment, facilities and applications. In general, a basic equipment inspection should involve the following:
- A task list or checklist based on a defined strategy or intent for the inspection
- An overall visual inspection of machine functionality and components
- A safety check, including failsafe functionalities
- Operation observation
- Wear assessment
- Recommendations for near-, mid- and long-term maintenance steps to address needs identified during the inspection
- Scheduling of any immediate maintenance tasks recognized during the inspection
- Documentation, including an inspection summary and report
As you can see, industrial machinery health inspection should not be treated as an ad-hoc task or one carried out when it is convenient. By treating periodic inspections as part of an overall maintenance strategy, manufacturers are much better positioned to increase productivity and eliminate unplanned downtime— which we will discuss later in this article.
Who performs inspections?
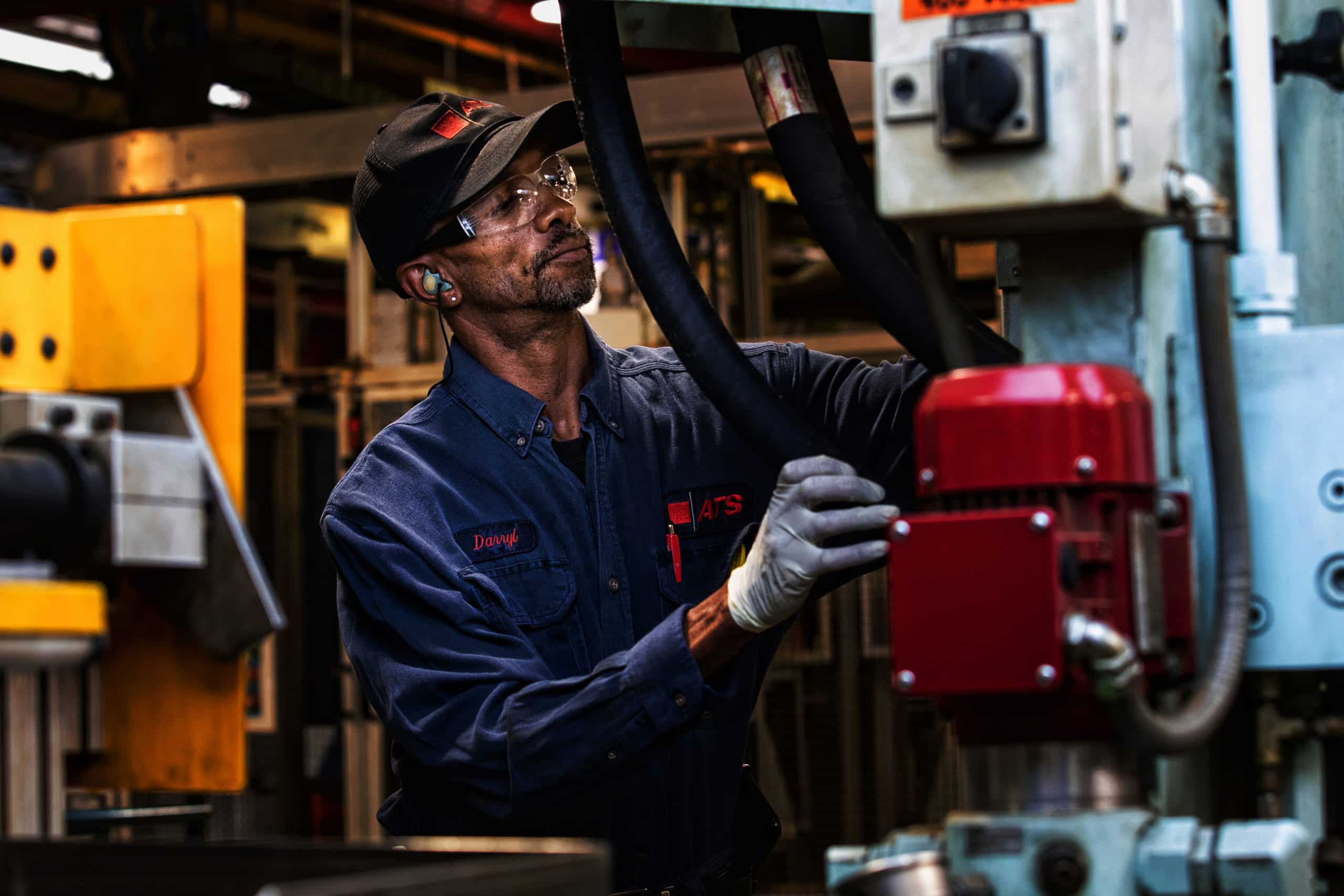
Inspections should be performed by trained, certified individuals with expertise in the field. An understanding of the equipment at hand, the processes, and applications it is used for, and the goals and objectives of the facility are key to complete effective inspections.
Note that while basic inspections can be carried out by equipment operators as part of everyday maintenance checks, it is important that machine inspections be conducted with the intent of a purposeful maintenance strategy — as illustrated by the depth of the tasks listed above.
When should machine inspections occur?
Comprehensive equipment inspections should occur at least once a year. In most cases, a twice-yearly inspection will yield tangible maintenance benefits that can justify the cost. As mentioned above, machine health inspections should not be considered the same as standard everyday preventive maintenance tasks performed within the facility. Equipment inspection is a detailed task with specific goals and targeted results.
Creating an effective machine inspection checklist
Developing a checklist for machine inspections is crucial for ensuring that no details are overlooked during the process. Without a checklist, there’s a risk that certain elements of the inspection may be passed over or neglected, which can lead to serious repercussions. Although each piece of industrial equipment is unique and may have different safety requirements than others, in general there are several items that should be a part of every checklist:
- Visual inspection: The first step should always be for trained and experienced technicians to look at the machine’s parts. They should look for any signs that components are becoming worn out, rusting or misaligned.
- Checking controls: Control panels — especially emergency stop buttons — should be checked and verify they are working.
- Lubrication: Lubricant levels need to be checked, and any parts that don’t have adequate lubrication should be tended to as soon as possible.
- Inspecting electrical systems: Workers need to inspect electrical components for any indications of frayed wiring, loose connections and any other issues that could impact performance and lead to equipment failure.
- Calibration: Ensuring machinery is performing within expected tolerances is crucial for getting the most out of it. Any machinery that has fallen out of calibration should be brought back to within specifications as soon as the issues are detected.
- Record keeping: All machinery and equipment inspection activities and their findings should be noted through proper documentation. This helps prevent wasted effort as well as compliance concerns.
Benefits of machine inspection
Regular equipment inspections can yield a range of benefits for your facility. These would include:
- Increased reliability: With regularly scheduled health inspections, you will be better positioned to identify potential equipment issues, allowing you to address them and plan for them more efficiently and effectively. This proactive approach can lead to fewer equipment breakdowns and an overall reduction in unplanned downtime, increasing the reliability metrics of your equipment.
- Higher output quality: When equipment is regularly inspected and maintained, it will operate at peak performance more consistently — leading to an overall improvement in product quality, a reduction in part defects and rejects, and a reduction in rework and wasted effort and material.
- Greater insight into maintenance and repairs: A machine health inspection strategy will allow inspection personnel to have a better understanding of each individual piece of equipment, developing a deep knowledge of the unique aspects and quirks of a machine. In addition to generating more data points by which to plan your maintenance and repair needs, this strategy can provide the intangible benefits of reliable gut feelings about maintenance and performance.
- Longer machine life: When equipment is inspected and maintained according to a plan, it is less likely to break down or incur damage as a result of maintenance issues. The proverbial “well-oiled machine” should operate as expected for a much longer service life when it is part of a health inspection strategy.
- Increased employee safety: When maintenance requirements go unnoticed or unheeded until they become a major issue, the safety of equipment operators and facility personnel is at risk. Equipment breakdowns can create danger for the immediate area as well as the facility. Facilities that employ regular equipment health checks may often see an increase in employee safety, as well.
- Reduced maintenance costs: The investment in a machinery health inspection strategy will almost always pay itself back with dividends — reducing unexpected downtime, decreasing the need for costly emergency repairs and part orders, extending equipment service life, and improving inventory ordering and efficiency.
How machine inspection informs predictive maintenance
Predictive maintenance is essential for keeping industrial equipment online as long as possible. This approach involves performing maintenance tasks according to which equipment is most likely to fail without intervention. Inspections are a key element of this strategy, providing maintenance teams with important information about machine health so they can make the most informed decisions about how to prioritize work.
Armed with the data they collect from machine sensors and visual inspections, maintenance teams can pinpoint which equipment is at the highest risk of failure. This means any problems can be proactively dealt with before they have an opportunity to develop into something more serious that leads to downtime.
The importance of machine inspections for regulatory compliance and safety
Another critical area where regular machine inspection becomes important is regulatory compliance. Manufacturers often need to provide proof of inspections and maintenance activities to ensure they comply with any applicable regulations. In other instances, these inspections may be required to maintain certain industry certifications. Having a strong protocol for heavy equipment inspections in place can protect manufacturers in this regard and prevent red tape from interfering with their operations. This provides them with the framework they need to follow best practices for record-keeping inspection findings, training and audit preparation.
In addition, regular inspections help manufacturers maintain the safest possible working environment for their employees. Inspecting equipment catches minor issues before they lead to unexpected failures or malfunctions that can result in unsafe working conditions.
Who benefits from machine inspection?
Machine inspection can benefit any manufacturing or industrial facility. While expertise in equipment health inspections can be tailored across industries, applications and manufacturers, some of the industries where these services can be most effective are:
- Aerospace
- Automotive
- Building Products
- Consumer Packaged Goods
- Heavy Equipment
- Paper & Pulp
- Power Distribution
- Tire and Rubber
Machine inspection with ATS
With over three decades of experience in industrial maintenance, ATS offers machine health assessments to improve and extend the life of your critical assets.
For more information, contact ATS today.