Workplace safety — specifically industrial safety — is rarely ignored, but is too often neglected, underestimated or deprioritized despite the best intentions. Sometimes leaders believe if they have not had an OSHA recordable injury in a certain period of time, they are good. Consider this common quote from a former CEO of a major company: “the absence in accidents does not indicate the presence of safety”. In other words, are you good, or are you lucky?
Safety should remain at the forefront of your operations because it’s one of the most important factors in the productivity of your plant — and ultimately the success of your business. Statistics on workplace safety back this up, and also prove that the majority of unsafe conditions and actions in a facility are preventable.
Ideas to improve safety in the workplace
A commitment to safety is the first step in improving and maintaining a safe workplace. Get started with these workplace safety tips designed to help you create a safer environment for you and your workforce.
Lead the way — Creating a safety culture starts with leadership. Leaders foster a culture where safety is fully integrated into the business and is a core value where all employees are engaged and share responsibility. By demonstrating that you are passionate about the safety of your employees, they will be more appreciative of your leadership and more likely to comply with standards and policies. If you do not have the right safety culture, any efforts to improve may be frustrating.
Establish a safety management system — Do you have a process to identify and address safety hazards and concerns? Establish a system that includes inspections of the physical areas of the plant and observation to identify potential at-risk behaviors. The system should also include a training component to develop leaders and employees “eyes for safety”. Prioritize items found during inspections and observations by assigning a risk factor that includes probability and severity. Get employees engaged in the process of identifying actions needed to reduce the risk. Your success will rely on their acceptance of the solution. If employees are part of the solution, your long-term success will be greatly improved.
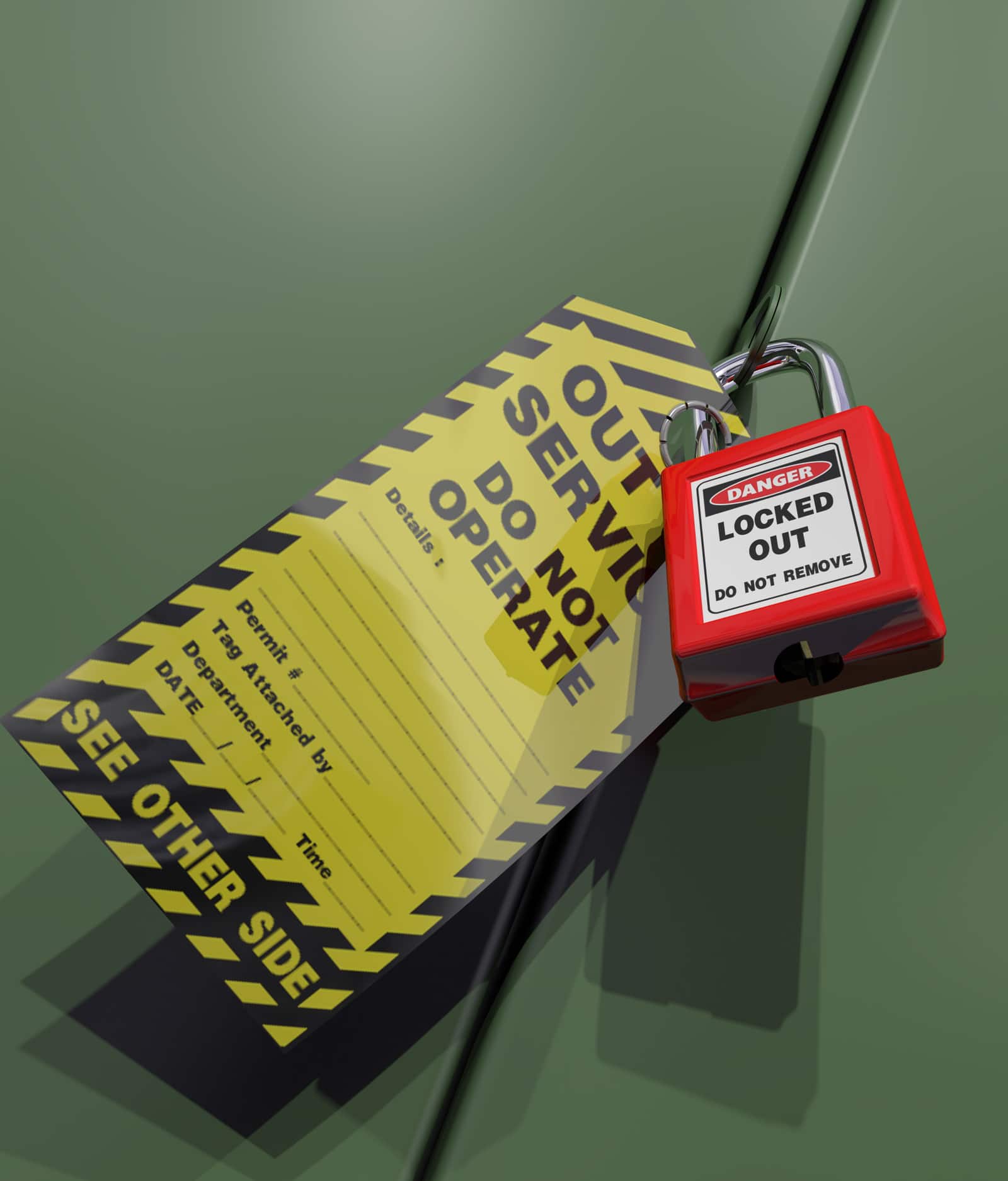
Some common hazards found in the workplace include:
- Missing or substandard machine guarding
- Slip/trip hazards related to poor floor conditions, clutter, material/liquid on the floor, etc.
- Workplace organization leading to aisles not clear, fire extinguishers and exit doors blocked, etc.
- Missing or substandard machine-specific lockout procedures
- Warning signs missing or not placed correctly
- Guardrail missing or not secured
- Pedestrian safety related to forklift traffic
Document and display — It is important to have key performance measures related to safety. These performance measures should focus on “leading indicators” that drive the “lagging indicators”. Lagging indicators are things you are trying to prevent (such as incidents) and leading indicators may be a series of measurements that give an advanced warning that the risk of an incident is increasing. An example of leading indicators may be a measurement of those processes that you are using to prevent incidents (inspections, observations, training, etc.). You should also keep employees informed of how hazards have been prioritized and the status of corrections.
Maintenance and safety
Manufacturing equipment maintenance is one of the most important components of a safe facility. Regularly maintained equipment and standard processes ensure that the factory floor remains as predictable and foolproof as possible. For more information on industrial maintenance solutions that can play a major role in your safety practices, contact ATS today.