Manufacturers are continuously striving to overcome challenges, improve processes and identify efficiencies, and the manufacturing trends that we see in 2025 are all service of these goals. As is typical throughout the industry, manufacturing industry trends are largely driven by technological advances, marketplace needs and the objectives of the business.
As we look ahead to the immediate future of the manufacturing industry, global supply chains continue to experience disruptions and automation is always making incremental moves forward, meaning that some of these trends will carry over — but there are brand-new challenges and opportunities ahead. From business agility to sustainability and the realities of adapting to what may be a “new normal,” the industrial manufacturing trends that may define 2025 are, in many ways, a response to the unique challenges of recent years. The ongoing march of technology, connectivity and automation enhancements is poised to continue solving problems and presenting unprecedented opportunities as well.
Read on to discover what we believe could be the top industrial manufacturing trends for 2025.
The top 10 latest trends in manufacturing technology for 2025
1. The continued rise of smart factories
Factories and manufacturing facilities are poised to pass the tipping point of smart factory adoption, moving from occasional or sporadic implementation of smart manufacturing equipment to more full-fledged systems, taking advantage of the full potential of data analytics and communication between machinery and central monitoring tools. Why? For several reasons:
- As older equipment continues to be phased out, newer machines come equipped with onboard sensors and monitoring tools.
- Manufacturers will be increasingly motivated to implement smart technology in order to keep pace with competitors who are seeing the benefits of the same.
- New developments in Industry 4.0 including enhanced machine learning capabilities and integrated systems for real-time data analytics are making it possible for manufacturers to make strides in terms of predictive maintenance and process optimization.
The costs of aftermarket sensors and other smart factory software and equipment continues to drop, while the benefits — more proactive and effective maintenance, greater insight into process efficiency, a reduction in overall operating costs — become ever-more apparent.
2. Increased focus on sustainability and carbon neutrality
As ESG — environmental, social and governance — issues become more of a concern for manufacturers, the importance of sustainable manufacturing processes and pursuit of carbon-neutral practices will become more prominent. In addition to sustainability requirements for government, municipal, and institutional contracts, manufacturers can expect to see more ESG requirements from commercial customers as well. At the same time, there is a growing interest in carbon capture technology and the ongoing integration of renewable energy in factory spaces. These are expected to drive even further advancements in sustainability for manufacturers.
3. Artificial intelligence and virtual processes
Technologies such as digital twins, machine learning, AI (artificial intelligence), AR and VR (augmented reality and virtual reality) are helping manufacturers become more effective and efficient by enabling remote monitoring, servicing and equipment operation — all without the need to be on-site. With communication approaching real-time, and the computing power to make it truly seem like the operator is in the room with the machine, virtual and remote operation is in keeping with other recent trends in manufacturing technology that enable access, flexibility and safety.
In fact, this technology has led to the development of so-called “dark factories,” which are those that are entirely automated. The widespread use of AR and VR in manufacturing is expected to make such facilities a more common element of many manufacturers’ operations. It’s expected that 2025 could see a leap forward in so-called “cognitive automation,” which uses advanced AI to optimize automation on the fly based on machine learning algorithms.
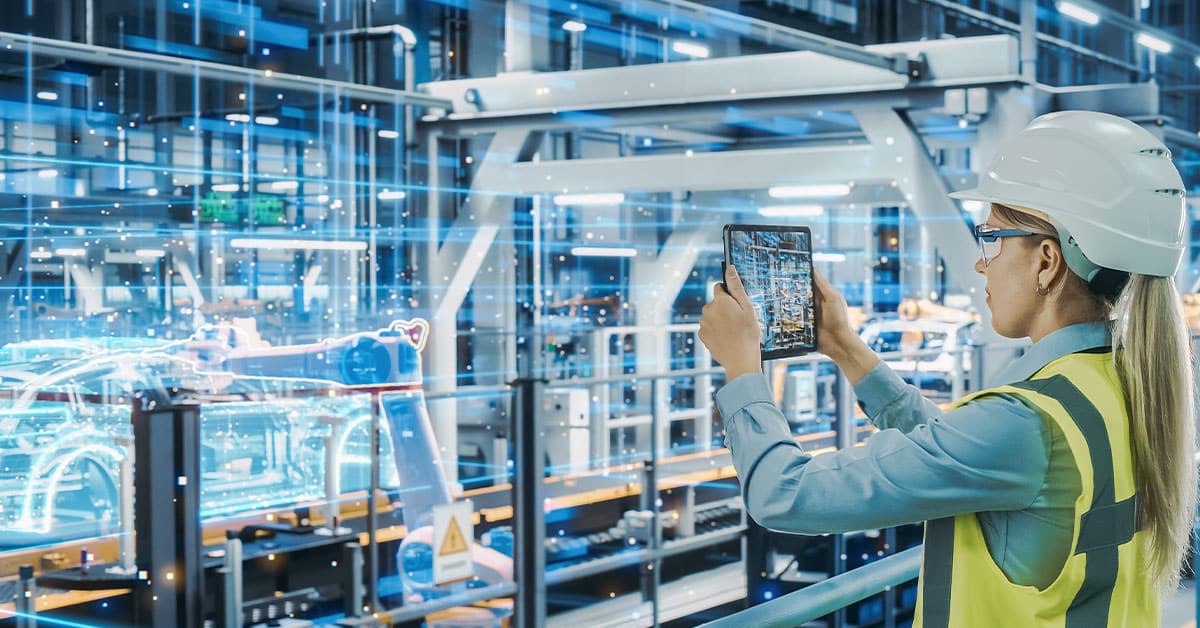
4. Data-driven maintenance as a margin enhancer
Sensors, remote monitoring, connected devices and the Internet of Things (IOT) have appeared on lists of digital trends in the manufacturing industry for the past several years and that continues this year. Why? On one hand, sensors continue to become more commonplace, communications are even faster and more reliable, and manufacturers are innovating more effective ways to use data to drive predictive maintenance. More effective, efficient maintenance is crucial given the financial hardship that many facilities faced in the last few years and may continue to face in the near future. Since predictive maintenance can vastly reduce unplanned downtime, creating material cost savings is now more important than ever.
The emergence of 5G networks now gives manufacturers the bandwidth and speed necessary to deliver more information from devices to the central server. Armed with this knowledge, it’s possible for them to do even more to prevent costly downtime. New predictive analytics tools also have the potential to help manufacturers optimize the lifespan of their equipment and keep it online for longer than ever before.
5. Supply chain reassessment
The initial worldwide supply chain disruption of 2020 continued to make waves in the subsequent years, driving home just how precarious the normal status quo has been for nearly every facility and business. Thus, it is unsurprising that in 2025, the supply chain continues to hold a prominent position as an area for continuous monitoring, management, and improvement, with facilities seeking creative ways to add flexibility and reliability while also retaining value. Data is one such means, with data-driven inventory management as an effective way to identify previously unknown supply chain efficiencies. Manufacturers can use data to more quickly adapt to the uncertainties of the supply chain landscape and work to minimize disruptions, which continue to be unpredictable. Utilizing the blockchain to manage this data brings traceability, while the advent of real-time supply chain tools can help manufacturers stay on top of everything. Supply chain resilience and flexibility strategies such as diversified sourcing and automation are expected to be especially relevant in the near future, as well.
6. Changing focus from B2B to B2C
Advancements in new manufacturing technology and supply chain strategies are making it possible for many manufacturers to reconsider their relationships with consumers. Rather than relying on retailers or distributors to serve as the middleman, many manufacturing companies today are selling their products directly to the consumer through e-commerce platforms and other methods. Emerging technologies in manufacturing such as smart factories also enable greater customization options today, which creates new opportunities for manufacturers to connect directly with consumers. With more people than ever doing their shopping online, this ongoing shift away from B2B to B2C should only become more prevalent in the coming year.
7. The ongoing importance — and permanence — of reshoring
In the recent past, reshoring was often presented as a lofty goal for the manufacturing sector, illustrating a renewed focus on quality, service and fulfillment speed. In the last few years, the importance of doing business closer to home was thrown into sharp relief, with reshoring becoming a necessary way to bolster continuity — not simply a buzzword. In 2025, reshoring is settling in as a more feasible and necessary supply chain solution, evolving beyond a response to a temporary challenge to become a more conventional way of operating. Ongoing geopolitical shifts further underscores the need for reshoring as a strategy in the near future.
8. Employee safety and health
Always a primary concern, employee safety is not often viewed as a “trend” so much as something that should be observed and fostered every day. This has led to the adoption of new ways of monitoring and maintaining employee health that are as important for your workforce as they are for your business. Some facilities are choosing to employ more advanced equipment to monitor employee locations, movement and even temperatures to track injury risk and illnesses. Wearable devices backed by AI-enabled analysis are expected to give manufacturers even more insights into the safety of their employees in the years to come.
9. 3D printing and additive manufacturing
3D printing technology and other additive manufacturing technologies have come a long way in recent years, becoming far more accurate, flexible and cost-effective than ever before. This is expected to be one of the most significant changes in the manufacturing industry well into the future. Not only does it allow for rapid prototyping and greater customization of products, but it also has the potential to make maintenance and repairs much faster and easier. Technicians may be able to print a replacement part in a fraction of the time it would take to source parts from a warehouse, cutting downtime to a minimum.
10. Meeting increased demand with a decreased labor force
Concerns about the labor force combined with existing industrial industry trends in the landscape means that manufacturing companies must be more efficient and nimbler than ever in addressing the skills gap and labor shortages. This requires a top-to-bottom evaluation of all production processes, identifying ways to increase efficiency and support the workforce while bridging the skills gap and providing cutting-edge technical training to meet today’s needs. Leveraging new manufacturing technology such as augmented reality and AI-driven training platforms may be the answer for bringing new employees up to speed as quickly as possible.
11. Cybersecurity in manufacturing
As IIoT technology continues to gain footholds in the manufacturing sector, there will be an increased emphasis on protecting the data used by these systems. Cyberthreats targeting industrial control systems and operational technology networks are on the rise, and security measures have to take a step forward in kind. Some of the tools manufacturers are expected to use in the coming years include zero-trust architecture, AI-driven threat detection and advanced encryption.
Some of these trends build on those with which you may be familiar from past years, and some are new as a result of today’s unique challenges.
As a technology-driven maintenance company, ATS can help with your goals and objectives to grow your operations this year and beyond. For more information, contact us today.