Reshoring has been one of the top manufacturing trends discussed over the past decade. In the last three years, however, the idea of reshoring has taken on a new immediacy, even urgency, with manufacturers re-examining reshoring as a business tactic in light of the lessons learned through the global chaos of the pandemic — and the lingering aftereffects of uncertainty.
What is reshoring in manufacturing? The term refers to the practice of bringing offshore production processes – those carried out in a country other than a manufacturer’s home country — back to domestic facilities.
As manufacturers examine the advantages of reshoring — along with the disadvantages — global factors, as well as the newfound prevalence and accessibility of smart factory technology, are making reshoring much more than the buzzword that it once seemed to be. Reshoring now offers a very real potential for increased stability, control, reliability and quality — and ultimately, overall cost savings.
Why are companies reshoring?
Companies are reshoring for a range of reasons:
- More confidence in the supply chain
- Increased domestic cost efficiency through smart factories
- Improved quality and innovation
- Contributing to re-strengthening the power of domestic manufacturing
On this last front, the positive contributions and effects of manufacturers taking reshoring steps are already being seen: according to a federal report, more than 1,800 companies reshored in 2021, resulting in over 261,000 new domestic jobs. Since 2010, that adds up to over 1.3 million reshored jobs, and reshoring now regularly exceeds foreign direct investment (FDI) by 100%. The numbers show that the benefits of reshoring are tangible, and here to stay — and we will explore these benefits further in the next section.
Advantages of reshoring
Reshoring offers numerous advantages, several of which have been mentioned here already. In this section, we will examine these advantages in greater depth.
- More confidence in, and control over, the supply chain: With reshoring, the supply chain is less subject to the ever-shifting winds of global economic and sociopolitical factors. While supply chain components several steps upstream may remain offshored by necessity, bringing even some upstream production closer to home can yield vast benefits in forecasting, cost management and adherence to deadlines and production commitments.
- Increased domestic cost efficiency through smart factories: With smart factory technology supporting workers by creating increased speed, productivity and throughput, manufacturers are able to vastly improve cost-efficiency, producing increased value
- Improved quality and innovation: Domestic production enables greater control over quality control processes and facilitates increased flexibility in developing new solutions and products.
- Contributing to re-strengthening the power of domestic manufacturing: The unabated offshoring of manufacturing jobs that occurred over several decades threatened to erase this critical sector of the middle class — and began to pose a threat to the ongoing viability of American manufacturing itself. With reshoring, manufacturing companies are bringing these jobs back and helping to strengthen the domestic economy at large, as well as the manufacturing industry specifically, contributing to the “rising tide” that lifts all ships.
Disadvantages of reshoring
While the benefits of reshoring are numerous and well-documented, there remain several considerations for implementing reshoring, including potential drawbacks and disadvantages. Some of these disadvantages can include:
- Cost of implementation: With a reshoring manufacturing plan, jobs and processes that once took place overseas will now occur in a “home” facility — which will almost always mean that additional space and infrastructure are required. This means capital investments in buildings, equipment, hiring and more, which can be significant. As with any business investment, the ultimate goal is to see a return on that outlay, but the upfront costs must be considered.
- Increased direct costs: The primary cause behind the offshoring drive was a vastly reduced cost of labor. That fact remains unchanged, although the gap is somewhat less significant, for a number of reasons. Labor costs have risen, even in traditional offshoring locations, and smart factory technology enables manufacturers to see much greater value and output from employees. While, again, the intent behind an investment in reshoring is to see a return on that investment, organizations will see increases in labor costs.
- Process changes: Reshoring will often mean a completely new way of doing things for manufacturers, even if underlying processes remain the same. In order to see the greatest benefit from reshoring, organizations will need to examine their processes, which will almost always result in changes. Aside from the time and effort required to define these changes, this will also require retraining and, potentially, personnel changes.
- Vendor and contract considerations: The working relationships between domestic manufacturers and offshore partners are almost always based on a contract agreement, which may run over several years. Offshoring may thus not be a decision that an organization can make right away, which may in turn add to logistical complexity in developing a beneficial strategy.
Reshoring and the supply chain
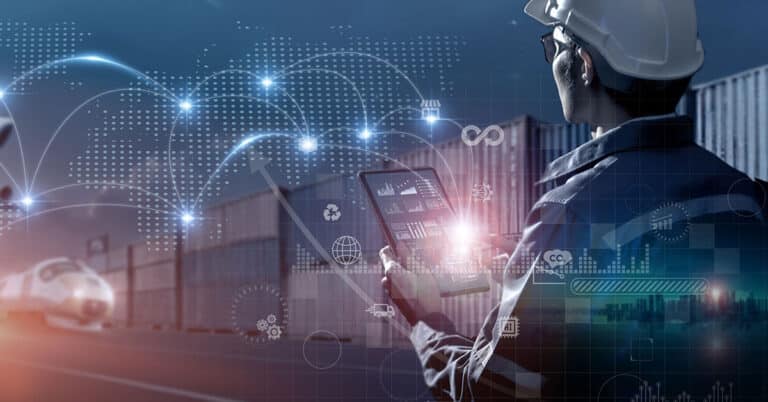
The supply chain is often one of the primary areas of benefit mentioned when talking about reshoring, and has been, in turn, one of the areas most significantly impacted by COVID-19, both in the near- and long-term. In fact, while the day-to-day work in manufacturing facilities has largely returned to normal, supply chain remains the primary area of ongoing uncertainty — exacerbated by global economic and sociopolitical concerns, including the war in Ukraine, uncertainty about U.S.-China relations and increased ecological considerations.
In practice, these issues mean that the supply chain is subject to delays, unpredictable costs, gaps in availability and other issues that can slow down production, reduce availability and increase costs, which manufacturers must either absorb or pass on to customers.
Reshoring manufacturing helps improve the supply chain management system in a number of ways:
- Reducing the impact of global macro factors: When production is moved back to domestic facilities, that means one — or more—– fewer links in the supply chain that can be impacted by factors out of the control of the organization, such as international conflict, as well as scenarios like adverse weather.
- Improved supplier relationships: With offshore and outsourced production, management from the “home” and the offshore facility may only meet in person once or twice a year, and communication of any type may be sparse. Reshored production, even if outsourced, allows for greater attention to building supplier relationships, which can help with costs, quality and the overall effectiveness of the working relationship.
- Better quality control: Reshoring allows manufacturers to improve production quality with an increased level of labor quality and more control over the processes and technology in use. Bringing production into domestic facilities also reduces or eliminates complications around differing international quality standards, streamlining logistics and management processes and helping to improve productivity and reduce costs over time.
Reshoring vs. nearshoring
Reshoring and nearshoring are similar strategies that can offer many similar benefits. The right choice for a given organization will depend on its current situation, its ongoing needs and its ability to make upfront investments.
Essentially, while reshoring involves bringing processes back to the organization’s base country, nearshoring involves bringing those processes closer to home, but not necessarily in the same country. Instead of eliminating many of the concerns described above, such as supply chain instability, reshoring can reduce their impact and likelihood, providing incremental benefits that, just like reshoring, can provide a positive return over time.
Reshoring vs. offshoring
Reshoring and offshoring are essentially two opposite strategies, many details of which have been explained here. In this section, we will list some of the defining characteristics of each strategy.
Reshoring:
- Production occurs in the same country in which the organization is based
- May be outsourced, provided that the outsourced facility is in the same country as the organization
- Brings processes and jobs that had previously been offshored back to the organization’s “home” country
- Requires increased up-front and direct costs, but can yield benefits in quality, reliability, supply chain control and overall costs
- Is supported by advances in smart factory technology, including industrial sensors, collaborative robots, AI and more
Offshoring:
- Production occurs in a country other than that in which the organization is based
- Traditionally relies on much lower labor costs as a primary benefit
- Production may be outsourced or may occur in facilities owned and managed by the principal organization
- Traditionally involves a tradeoff between quality and cost
- Is subject to global economic, social and political factors which can cause delays and impact overall costs
Reshoring considerations
As mentioned earlier, reshoring should involve a number of considerations when under development as a strategy. Here, we will examine those considerations further:
- New or renovated facilities: As mentioned earlier, the capital costs of new or refurbished facilities — whether purchased or rented — can be significant in the immediate term, even though the investment can pay off over time. Manufacturers must identify the processes that they are reshoring, acquire the necessary space and then move on to acquiring equipment.
- Factory planning: Equipment purchase or rental should only occur once factory planning has been carried out, identifying optimal workstreams, equipment placement and supporting processes. Factory planning takes time and requires the expertise of specialists in this area.
- Updated maintenance strategies: With new processes and equipment in place, manufacturers must develop the right maintenance strategies to keep processes running efficiently and productively. With more equipment on hand, strategies like predictive maintenance become more important than ever, with the goal of increasing uptime and ensuring that equipment is creating value.
- Leveraging technology to produce ROI: Industry 4.0 and IIoT technologies are among the major factors in the increased viability of reshoring, as they increase speed and efficiency, offer unprecedented insights into production, and help workers perform higher-value tasks. Companies that are reshoring must take these technologies — often, the underpinnings of building a smart factory — under consideration when developing a plan in order to ensure that they gain as much advantage as possible from taking these steps.
You now have an understanding of the reshoring movement, why it is occurring and the benefits that it can provide. By weighing these benefits against the potential disadvantages, and applying them to your own processes and scenario, you are ready to start making a decision about the best way for you to proceed.
Check out how ATS quickly filled skilled labor gaps for a leading CPG manufacturer at their FDI greenfield facility.