The global COVID-19 pandemic had, by all accounts, a significant impact on the manufacturing sector worldwide at its peak. Amid uncertainty and an abundance of precaution, all but the most essential facilities were forced to shut down for not only health and safety reasons, but a decrease in demand as global economies slowed. Even facilities that were able to remain operational did so at a lower capacity in order to maintain social distancing best practices.
As economies recover and demand steadily grows, manufacturing facilities have been and will continue to be able to re-open and ramp up production. The post-pandemic landscape will bring with it major challenges, as well as opportunities — both of which will require new investments in manufacturing technology to address. Below, we will look at why manufacturing tech will be more important than ever post-COVID; how new manufacturing technology helps companies meet demand and keep up with growth; and what types of manufacturing technology you should consider implementing at your facility.
Investments in manufacturing technology to meet demand
As global economies reopen, it will be critical for manufacturers to keep up with demand. New manufacturing technology will play a key role in their ability to do so.
Manufacturers will face changes such as:
- Fast turnaround and fulfillment requirements: As economies approach a return to normal — albeit a “new normal” — demand will ramp up quickly. Manufacturers may be forced to fulfill orders under tighter deadlines than they are accustomed, or risk losing income to competitors. Manufacturing technology can help to meet those needs.
- Continued remote and distanced work: Even as facilities reopen, many health and safety precautions will remain in place. Key among these are social distancing practices. In-person workers must maintain sufficient space from one another, and remote work may become more prevalent when feasible. Technology can ensure that effective, efficient output remains possible under these conditions.
- An increase in reshoring: As the pandemic peaked, many global supply chain shortcomings were exposed. In response, manufacturers can expect plans for rapid reshoring, as the need for a reliable domestic supply chain is now starkly clear. With the help of new manufacturing technology, 2020 may see one of the biggest increases in reshoring in recent memory.
- Economic challenges: Throughout the first half of 2020, facility shutdowns and slowdowns have presented major economic challenges to manufacturers. Even as demand begins to grow, there is an uncertain path forward — in recovering from the lost business of the early pandemic, and in returning to previous income levels.
The manufacturing technologies that will help facilities rise to meet the challenges of these changes include:
- Automation: Automation continues to become “smarter,” more effective, integrated and inexpensive. The use of automation — in conjunction with the innovation that can only be provided by people — will be critical to meeting more demanding production requirements.
- Remote work tools: From video conferencing to more advanced technology such as virtual reality and augmented reality, remote work technology will facilitate safe distancing practices — whether in the plant or working off-site.
- Sensors: Smart, connected sensors are among the fastest-growing pieces of equipment in manufacturing, and will play a major role in the future of manufacturing technology. Sensors aid in production and maintenance practices, enabling more efficient processes in these areas that can increase speed and efficiency while also production reducing costs.
Now let’s take a deeper dive into the benefits of sensor technology.
The role of IIoT sensors in the future of manufacturing technology
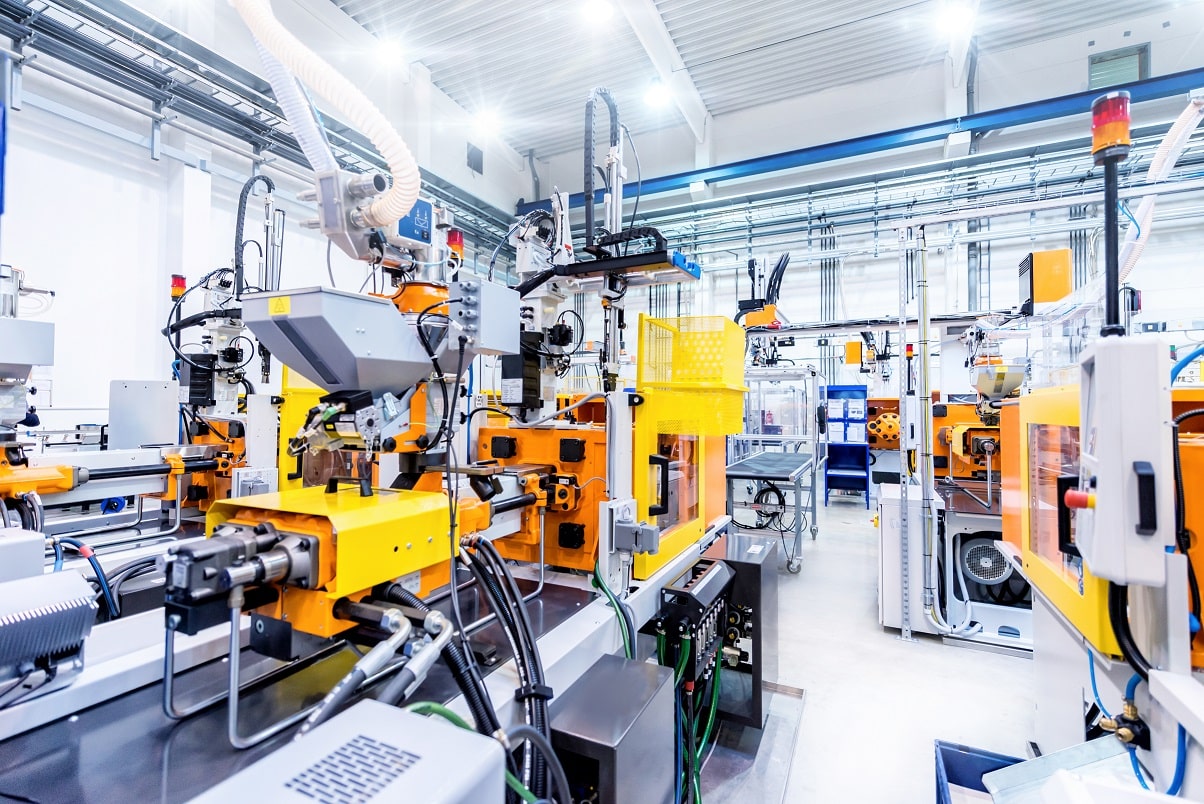
IIoT (Industrial Internet of Things) sensors will undoubtedly be present in the most successful manufacturing facilities, large and small. Here, we will look at what sensors do, and why they are a worthy investment:
- More effective maintenance: With real-time, round-the-clock monitoring of manufacturing processes — including advanced details such as vibration and heat monitoring — sensors can provide maintenance personnel with previously unheard of analytics. More effective maintenance allows you to improve OEE, reduce downtime, prevent unexpected shutdowns, and conduct maintenance when it is most convenient and the least disruptive — all of which lead to better productivity for your plant and lower maintenance costs.
- Improved inventory management: Inventory sensors increase the accuracy of spare parts counts, and help assure that a part is on the shelf when it is expected to be. Sensors also aid in more efficient ordering, meaning that replacement parts and components are stored in optimal conditions (such as temperature and humidity). These efficiencies reduce or eliminate the need for emergency part orders, and can make certain that no more time is wasted rectifying inventory errors.
- Increased safety: Sensors provide data and intelligence from the hardest-to-reach parts of machinery, which are the most revealing when it comes to the health of the equipment. In some instances, it is difficult and dangerous, if not impossible, for a person to reach these areas, hence why sensor technology plays a role in improving safety for your workers.
At ATS, we offer comprehensive maintenance services incorporating the latest in manufacturing technology — including sensors and other “smart,” connected equipment. We can not only implement the right sensors and other Industry 4.0 technologies at your facility, but also offer our expertise in data collection, management and analysis, ensuring that the correct maintenance actions are taken in response to the intelligence drawn from the sensors.
With over three decades of experience in industrial maintenance and MRO asset management, ATS is committed to making your factory run smarter and better. For more information on all our service offerings, contact us today.